This is topic MM Full Length Subframe Connectors are on (Pics included) in forum General Talk at Northern California Ford Owners .
To visit this topic, use this URL:
https://californiafords.com/cgi-bin/ultimatebb.cgi?ubb=get_topic;f=1;t=036987
Posted by Luke87GT (Member # 21) on
:
I finally got my pics uploaded after having the Maximum Motorsports Full Length Subframe Connectors installed on my '96 Cobra.
My good friend Andrew (Cafords user name: QuickSparks #8826) brought over his welding equipment and made a house call for me. If anyone needs welding work done (subframes, torque boxes, roll cages or even none-automotive work), I highly recommend Andrew as he has a lot of welding experience and all the proper equipment, not to mention he is a Ford nut. He can do house-calls or the work can be done at his shop in Benecia and his prices are very reasonable.
Here are some pics of the job:
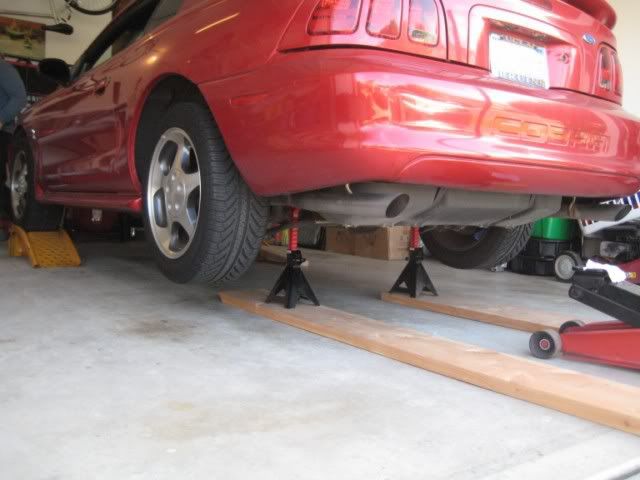
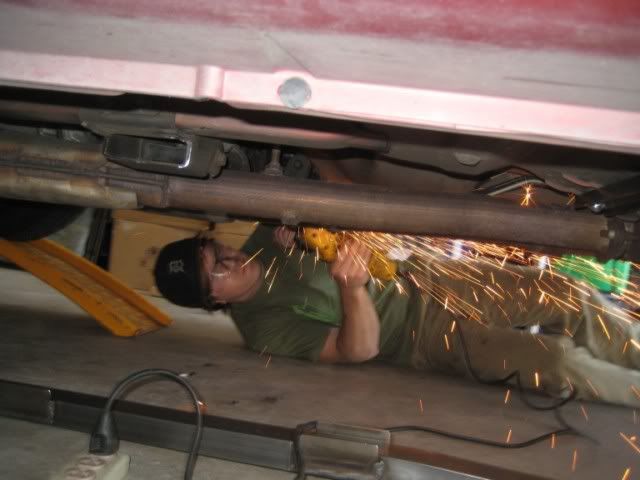
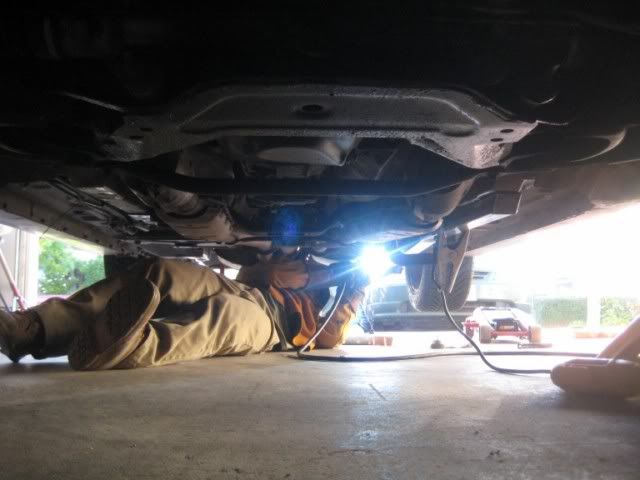
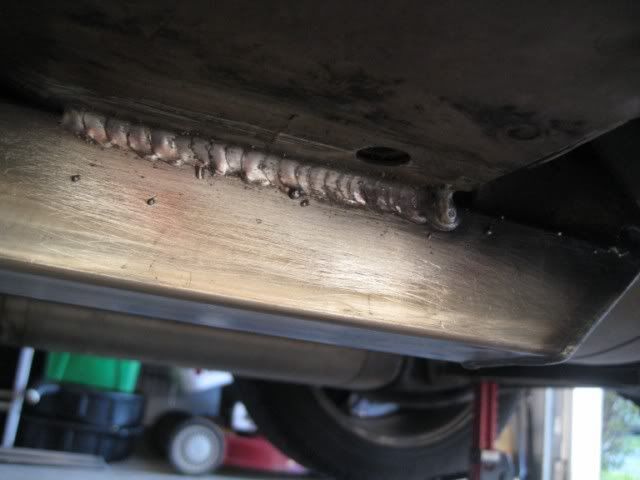
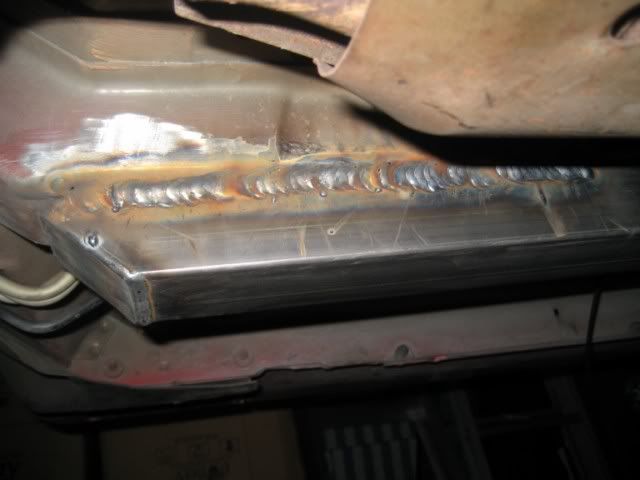
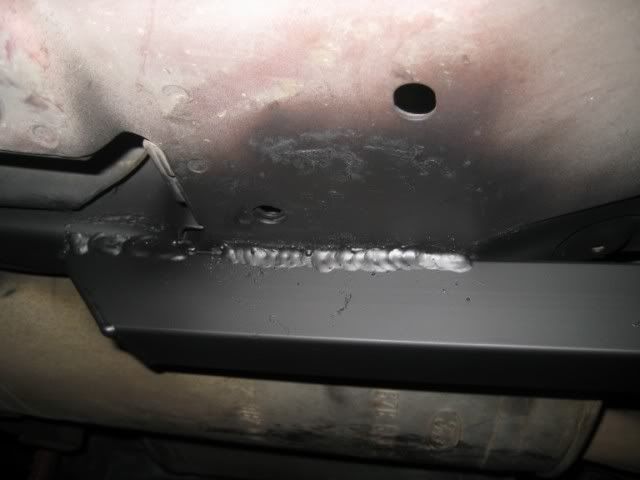
Posted by Blind (Member # 3052) on
:
nicely done, I love them on my 97, didn't notice as huge of a difference as I did when I put them on my 89 though
Posted by 427 StRoKeR 94 GT (Member # 8722) on
:
Nice job looks good
Posted by 90gtvert (Member # 8697) on
:
Damn you got his number I need a house call
Posted by PugOwner (Member # 8404) on
:
Not a good idea to have the car on stands when doing this. The car should be resting on it's wheels, so the body has zero flex.
Posted by Luke87GT (Member # 21) on
:
quote:
Originally posted by 90gtvert:
Damn you got his number I need a house call
I will ask Quicksparks to PM you.
quote:
Originally posted by PugOwner:
Not a good idea to have the car on stands when doing this. The car should be resting on it's wheels, so the body has zero flex
You are correct in the suspension must be loaded when welding in subframe connectors. The car was on ramps in the front, and the jack stands were over the axle tubes in the rear. In other words the suspension was loaded before we started any welding.
Posted by mustang928 (Member # 2123) on
:
Those are some nice welds... what welder did he use??
Posted by QuickSparks (Member # 8826) on
:
quote:
Those are some nice welds... what welder did he use??
Thanks. I used a Lincoln MIG welder with 75% argon, 25% CO2 shielding gas.
Posted by NCALSVT (Member # 3205) on
:
quote:
Originally posted by QuickSparks:
quote:
Those are some nice welds... what welder did he use??
Thanks. I used a Lincoln MIG welder with 75% argon, 25% CO2 shielding gas.
what settings?
Posted by QuickSparks (Member # 8826) on
:
quote:
what settings?
I set the voltage for the thicker MM subframe connectors (about 0.120" wall) and keep more of the heat in the connector rather than the thin subframe.
Posted by 510vnum (Member # 9106) on
:
nice welds
Posted by SPTVENM (Member # 7080) on
:
coo
Posted by QuickSparks (Member # 8826) on
:
quote:
nice welds
Thanks!
Posted by NCALSVT (Member # 3205) on
:
quote:
Originally posted by QuickSparks:
quote:
what settings?
I set the voltage for the thicker MM subframe connectors (about 0.120" wall) and keep more of the heat in the connector rather than the thin subframe.
I meant the settings on the welder itself
Posted by RRRCobraSC281 (Member # 7086) on
:
I think it's going to really depend on your welder.
Posted by NCALSVT (Member # 3205) on
:
quote:
Originally posted by RRRCobraSC281:
I think it's going to really depend on your welder.
I got the same one
Posted by poisonpony96 (Member # 3942) on
:
quote:
Originally posted by NCALSVT:
quote:
Originally posted by RRRCobraSC281:
I think it's going to really depend on your welder.
I got the same one
what model do you have? on my small lincoln it has on chart on the inside were you put the wire spools. it tells you everything you need to know. on mine i would have to run gasless for .120 wall and it would be set at d-3 now on mine d is the highest temp setting and 3 is on a scale of 1-10. hope this helps. plus once you use you welder you should find out what works best by how well your weld looks. did you see good penatration etc.. now i've never been to school but never had a problem yet. My welds look just as good as the ones in the pics.
Posted by QuickSparks (Member # 8826) on
:
The welder I used on Luke's MM subframe connectors is a Lincoln Electric SP-170T which is between 5 and 10 years old. Can't give you the exact settings I used that day because I always adjust the settings to suit the job based on the results I am seeing.
This machine just has five coarse voltage settings, called "A, B, C, D, E," and the wire feed speed is continuously variable. I have a good idea what voltage and wire speed I should use based on the thickness of the pieces I'm welding. Then I experiment on a piece of scrap to tune the wire speed so it sizzles just right. If I notice excessive overlap then I turn up the voltage and adjust the wire speed accordingly.
Posted by Luke87GT (Member # 21) on
:
quote:
Originally posted by QuickSparks:
The welder I used on Luke's MM subframe connectors is a Lincoln Electric SP-170T which is between 5 and 10 years old. Can't give you the exact settings I used that day because I always adjust the settings to suit the job based on the results I am seeing.
This machine just has five coarse voltage settings, called "A, B, C, D, E," and the wire feed speed is continuously variable. I have a good idea what voltage and wire speed I should use based on the thickness of the pieces I'm welding. Then I experiment on a piece of scrap to tune the wire speed so it sizzles just right. If I notice excessive overlap then I turn up the voltage and adjust the wire speed accordingly.
Did I mention the man can weld!
Posted by Luke87GT (Member # 21) on
:
Just an update on a small project from this weekend on my 96 Cobra.
One of my axle tubes was leaking a bit, so I had my buddy Andrew (QuickSparks is his screen-name on cafords) weld up my axle tubes.
No more leak, and no fear of twisting em
Here are a few pics. If anyone needs some weld work done, PM me and I will get you in touch with him (he is located in Benecia)
Thanks for the work Andrew!
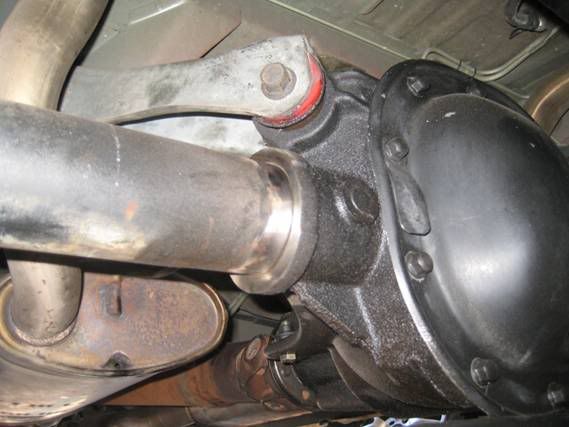

Posted by Duncan Motors (Member # 7045) on
:
good solid welds work with house calls he,ll stay busy for sure!how much for the axle tubes and for the sub frames?
Posted by JohnB (Member # 969) on
:
Right on Luke, glad to see he could take care of it!
Posted by Luke87GT (Member # 21) on
:
quote:
Originally posted by Duncan Motors:
good solid welds work with house calls he,ll stay busy for sure!how much for the axle tubes and for the sub frames?
Ya, I am one picky SOB, and this guy can certainly weld lol (Stick, MIG, TIG, steel, aluminum, whatever you need)...
I would PM him directly and ask him to quote you. His prices are very reasonable since he is just getting his business up and running.
QuickSparks - Member #8826
There are two people on this forum that I trust my automotive needs to: One is Quicksparks and the other is JohnB... Both great resources to have in the automotive community.
[ November 09, 2009, 01:05 PM: Message edited by: Luke87GT ]
Posted by turbo50 (Member # 6700) on
:
Can you please pm me his (quicksparks) phone number. Thanks.
Dan
Posted by snakebit95 (Member # 8871) on
:
Very Nice Luke! That is definitely on my "To do list".
Posted by Luke87GT (Member # 21) on
:
quote:
Originally posted by turbo50:
Can you please pm me his (quicksparks) phone number. Thanks.
Dan
PM sent.
Posted by turbo50 (Member # 6700) on
:
got it, thanks Luke.
Posted by QuickSparks (Member # 8826) on
:
Hi All,
Thanks for the compliments that have been given. Feel free to PM me directly to discuss your project and to get a quote.
I strongly prefer to do the work in my shop in Benicia, but I can make house calls if your location meets a few requirements.
Posted by phil a (Member # 6951) on
:
Looks good. I may be mistaken, but I always thought that the rear end had to be removed from the car before welding up axle tubes to ensure that everything was at a perfect 90 to each other
Posted by Luke87GT (Member # 21) on
:
quote:
Originally posted by phil a:
Looks good. I may be mistaken, but I always thought that the rear end had to be removed from the car before welding up axle tubes to ensure that everything was at a perfect 90 to each other
Yes, the tubes were welded up with the rearend in the car and the suspension unloaded. Many people have told me to never attempt to weld without a jig where a metal rod slides through each axle tube to keep it straight. Although that is the best way to do it, keep in mind that the axle tubes slide into the differential housing by something like 2-3inches.
Knowing this, we tacked the tube to the housing in 3 regions, 120-degrees apart, and connected them with beads. Once one bead was laid, we went to the other side to let the first side cool. Everything turned out well.
The key is to go slow... Lay down the tacks to keep everything together and keep it cool.
Posted by QuickSparks (Member # 8826) on
:
This is a customer's Ford 9 inch differential housing from a 65 Mustang. These things did not come stock with any way to drain the oil, so the customer had a bung welded in the bottom with a pipe plug so he could easily drain the oil.
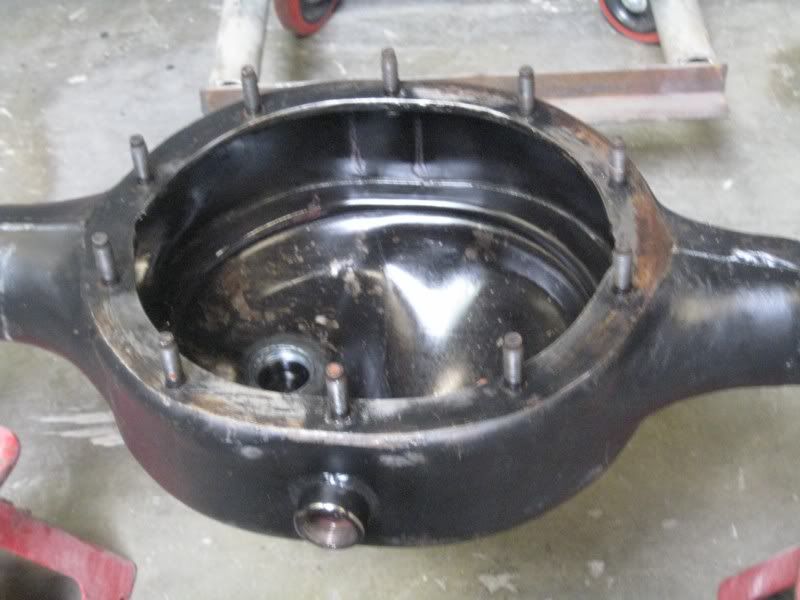
When he was lifting the car, the jack pressed on the welded bung, which put a lot of stress on the ¼” plate that the differential housing is made of and deflected it inward. As a result, the bung was misaligned from the housing. I used a rosebud tip to heat the plate around the bung, then banged it out with a hammer to straighten it. Here's what it looked like when it was crooked:
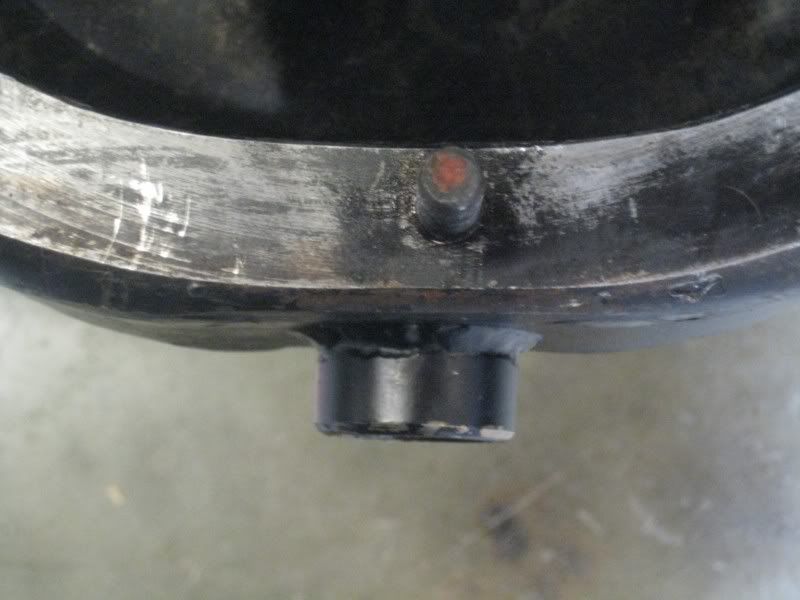
This is the piece of ¾” steel plate that I fabricated to support the load of the car when using a jack to lift under the differential housing.

Here is the jacking plate fitup before welding:
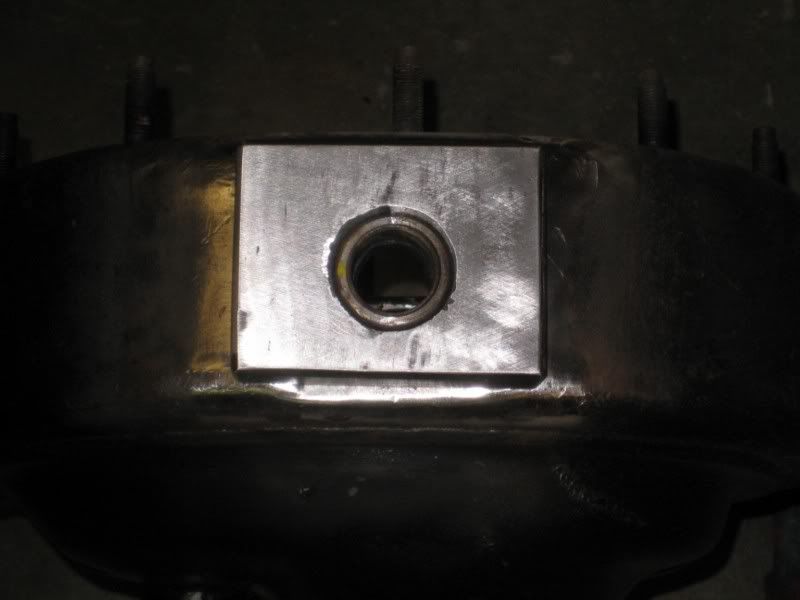
Here is the jacking plate TIG welded in place.
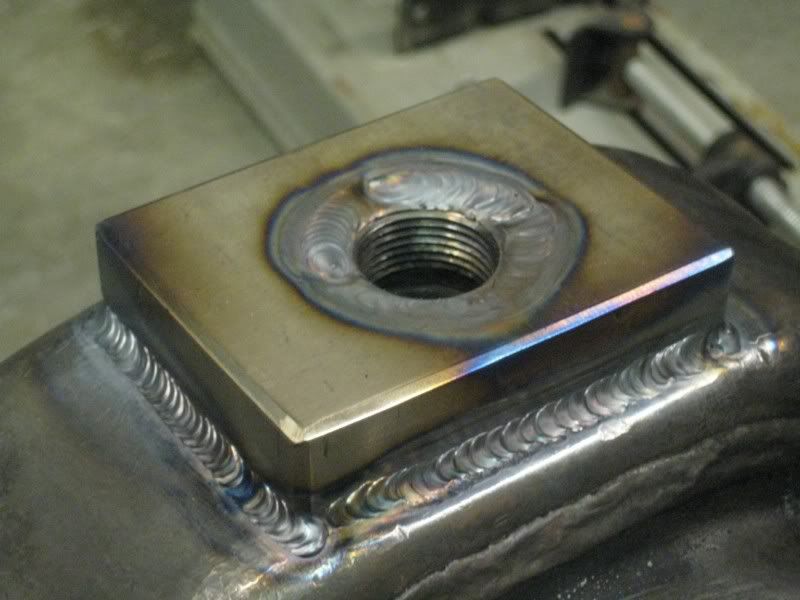
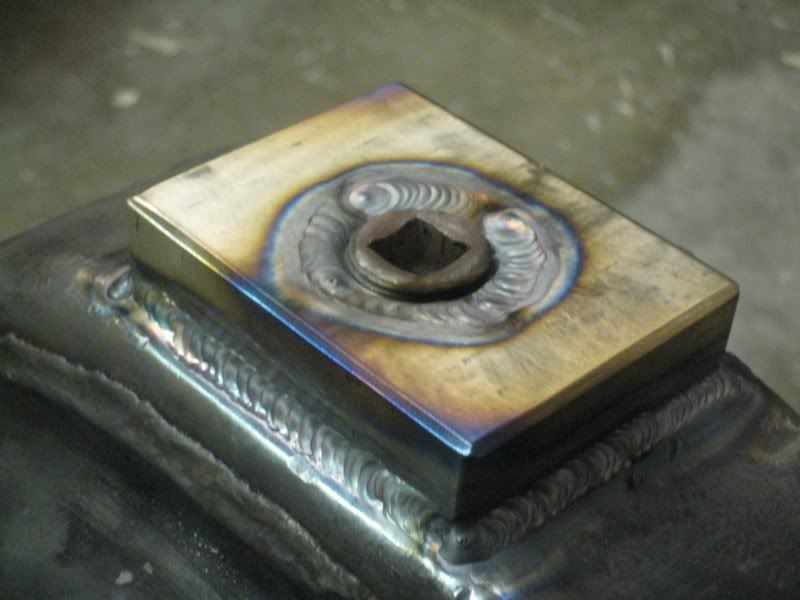
Posted by phil a (Member # 6951) on
:
I'm sitting here smiling like an idiot - look at that fab works and the welds!!
Awesome
Posted by Luke87GT (Member # 21) on
:
Andrew, those Tig-beads are phenomenal!
Although most 8.8inch aftermarket diff covers place the bung at the bottom of the cover to avoid the need for a jacking plate. Interesting that they did not think of this with the 8" or 9"
In any case, great job!
[ November 12, 2009, 05:45 PM: Message edited by: Luke87GT ]
Posted by QuickSparks (Member # 8826) on
:
Thanks Phil, Luke.
The construction of the 9 inch is completely different from that of the 8.8 inch. The 9 inch is made of formed sheet metal and the 8.8 is cast iron. If you placed a drain at the bottom of the back cover on the 9 inch, there would still be a 3/4" deep reservoir of oil below the level of the drain plug. I think that's why people put the drain directly on the bottom of the 9 inch rear.
Fueled by Ford Mustang Owners
on CaliforniaFords.com